In the previous post of our blog series 'The Edge of Reality,' we took a closer look at the design of the entire experience of an XR application. Key elements such as onboarding, storytelling, and ergonomic aspects played a crucial role. In this part of our blog series, we dive into practical experiences of XR technologies in the industry.
Recognizing applications of XR
The application of XR in the industrial sector is already wide-ranging. Reality is enriched with digital elements, and users receive additional information through virtual, auditory, or tactile inputs, supporting them as effectively as possible in their work processes. To use XR optimally, it is important to understand which senses are being engaged and what makes sense for the specific customer. Requirements must be clearly defined, and use cases need to be worked out. Information should be delivered exactly where it is needed. XR must be applied purposefully, and sensory overload must be avoided.
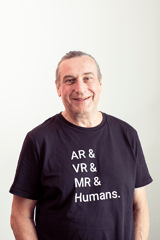
“A perfect blend of realities would be if you open a real screw on a real machine and then insert a virtual part. Service technicians could be on-site without ever having been there. With the many possible applications, the question arises whether our reality will be a Mixed Reality in the near future?!”
– Ulf Oberbichler, CEO, Alphagate
Training
One of the many possibilities is the use of XR for training. This can be done on an already existing machine or even before a machine is delivered. A format change can be practiced on an existing machine with virtual parts. Users who are new or not yet confident with a machine can be optimally supported and guided through the use of XR. The application guides them through the individual steps of the work process until they are familiar with the machine. Especially during the times of Covid, the use of XR has a big advantage. If shift workers or even an entire shift is out due to illness, other operators can step in, even if they don’t know the machine or don’t know it well enough.
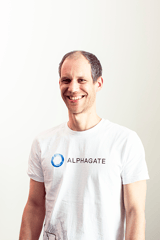
“Initially, the use of XR applications is somewhat fun, but that is not the key factor. Eventually, it becomes routine, and efficiency takes center stage. XR will definitely be the future. It is on the rise and becoming increasingly present. It will support operators, but not replace them!”
– Klaus Feurstein, Software Developer, Alphagate
"Operators no longer need to carry papers, pens, and cameras for documentation purposes. It is automatically recorded where the user was, what they looked at, and what the result was. Photos and checklists are automatically stored. This allows more time for other tasks. It is easy to trace how a batch was produced. Experienced users require a less detailed MR application and can use a tablet instead of smart glasses for checklist tasks. Users and service personnel are guided directly to the source of the error through alarm localization and can then fix it step by step.
Remote Support
By using smart glasses, operators can work hands-free, and remote support knows exactly what the users are seeing. This allows them to highlight objects and provide remote assistance. Taking it a step further, eye tracking makes support even easier. It shows whether the operator is looking at the correct object and can correct it if necessary.
Maintenance of the XR Application
An XR application is no more maintenance-intensive than regular visualizations. It is set up once and can then be used directly. When creating a recipe, additional spatial coordinates are added for localization, and everything else runs generically. For certain tasks, there are standard objects that are implemented once. In a recipe, the task (e.g., assembling, disassembling, taking photos, etc.), location, and additional information (images, videos, PDFs, instructions) are stored, and it can then be loaded.
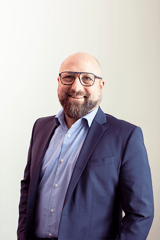
“It is important not to lose sight of the fact that by using the new technology, you can quickly achieve a positive effect – a quick win.”
– Johan Spets, COO, Alphagate
Added Value with XR?!
Is it just a nice gimmick, and because the technology is available, it is being used, or is it actually being put to good use? When implementing new technology, it must always be considered that it has a positive effect on employee motivation. They need to feel motivated and know that the company is making an effort and doing something for them. The use of XR should offer added value to the users. The smart glasses serve as safety glasses while also displaying additional information, thus supporting work processes. This would provide an incentive for users and increase acceptance.
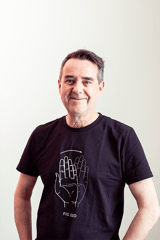
“It has to be a complete experience. At the moment, it still feels unnatural for users to interact with something intangible. Operator acceptance is essential—just like the added value.”
– Jürgen Mohr, Head of Innovation Product Management, Alphagate
A healthy balance between reality and extended reality is always needed. Users must not be overwhelmed with information but should be able to maintain a clear overview and receive optimal support in their work processes. The use of XR in industry must be carefully thought out—otherwise, it remains just a nice gimmick for the trade show.